Digital transformation is redefining the manufacturing landscape through technologies like AI, IoT, robotics, manufacturing data analytics and big data analytics. These tools help companies increase efficiency, reduce downtime, improve product quality, and drive innovation. In fact, manufacturers adopting advanced analytics report productivity gains of up to 30%.
However, challenges like high initial investment, workforce adaptation, and cybersecurity concerns can hinder implementation.
This blog highlights how leading manufacturers—Siemens, GE, Tesla, Boeing, and Caterpillar—are using analytics to overcome these barriers and set new industry standards.
1. Siemens: Smart Factories Powered by Digital Twins and AI
Overview:
Siemens is pioneering smart factory initiatives by leveraging digital twin technology, IoT, and AI to simulate and optimize production environments in real time.
Technologies Used:
Digital twins, IoT sensors, AI-powered analytics, smart maintenance systems.
Benefits:
- 20% increase in manufacturing efficiency through automation and optimization.
- Predictive maintenance reduces equipment downtime using real-time sensor data.
- AI-driven quality control detects defects during production.
- Agile assembly lines enable rapid adjustments and customizations.
- Sustainability gains via energy-efficient operations and resource optimization.
Challenges:
- Significant capital required for IoT, AI, and digital twin implementation.
- Need for upskilling the workforce to handle digital tools.
- Heightened cybersecurity risks due to interconnected infrastructure.
2. General Electric (GE): Harnessing the Industrial IoT with Predix
Overview:
GE uses its Industrial IoT platform, Predix, to collect and analyze data from industrial machinery, enabling smarter maintenance and resource use.
Technologies Used:
Industrial IoT, machine learning, cloud computing, predictive modeling.
Benefits:
- Transition from reactive to predictive maintenance strategies.
- 25% increase in productivity from better machine utilization.
- Improved energy efficiency drives down operational costs.
- Real-time inventory and supply chain visibility.
- Remote monitoring boosts workplace safety and responsiveness.
Challenges:
- High cost and complexity in modernizing legacy systems.
- Increased exposure to cyber threats across interconnected networks.
- Change management required to shift from manual processes.
3. Tesla: AI-Driven Smart Manufacturing
Overview:
Tesla revolutionized automotive production by integrating AI, robotics, and machine learning into its highly automated assembly lines.
Technologies Used:
AI, robotics, machine learning, real-time analytics.
Benefits:
- Rapid production cycles with minimal human intervention.
- Real-time defect detection ensures high product quality.
- Flexible manufacturing supports product customization at scale.
- Scalable processes meet surging market demand efficiently.
- Eco-conscious production reduces waste and enhances sustainability.
Challenges:
- High ongoing costs for robotics and AI deployment.
- Need for continuous innovation to maintain competitive edge.
- Complex decision-making in highly automated environments.
4. Boeing: Augmented Reality (AR) for Precision Assembly
Overview:
Boeing has transformed its aircraft assembly process by equipping workers with AR headsets that provide real-time visual instructions.
Technologies Used:
Augmented reality (AR), wearable headsets, interactive digital overlays.
Benefits:
- 30% reduction in assembly time.
- Increased precision and reduced rework in complex installations.
- Interactive AR tutorials shorten training cycles.
- Safer assembly processes guided by real-time automation.
Challenges:
- High initial investment in AR infrastructure.
- Requires specialized employee training for effective use.
- Compatibility and software performance can affect reliability.
5. Caterpillar: Data-Driven Predictive Maintenance
Overview:
Caterpillar uses embedded IoT sensors to collect operational data from its machinery, enabling predictive maintenance and improved fleet performance.
Technologies Used:
IoT sensors, analytics platforms, remote diagnostics tools.
Benefits:
- Anticipates breakdowns, reducing unplanned maintenance.
- Extends machinery life with optimized servicing schedules.
- Boosts energy efficiency and operational cost savings.
- Enables remote issue resolution without onsite intervention.
- Increases customer trust through dependable machine performance.
Challenges:
- Data volume and complexity require robust analytics infrastructure.
- IoT connectivity exposes systems to cybersecurity threats.
- Initial investment in sensors and data management platforms is high.
Summary Table: Transformation at a Glance
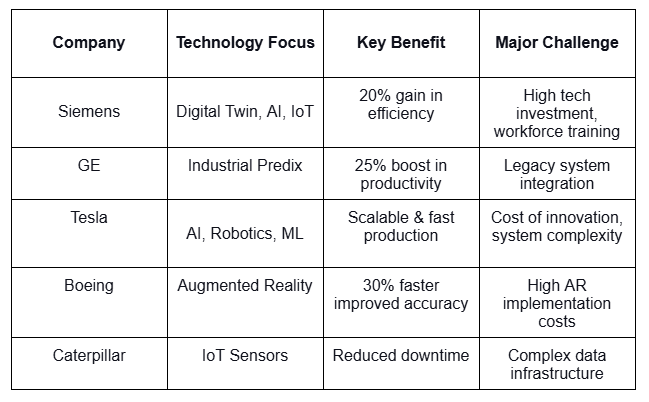
Future-Proof Your Manufacturing Operations
Manufacturing leaders like Siemens, GE, and Tesla are proving that analytics is more than a buzzword—it’s a strategic advantage. With the right tools and mindset, digital transformation can drive profitability, agility, and sustainability across your operations.
Want to see how advanced analytics can work for your business?
📅 Schedule a free consultation with Ascend Analytics to explore tailored solutions that modernize your operations and drive measurable impact.